Metallurgical Coal
What is Coal?
Coal formation began during the Carboniferous Period - known as the first coal age - which spanned 360 million to 290 million years ago.
Coal is a fossil fuel and is the altered remains of prehistoric vegetation that originally accumulated in swamps and peat bogs.
The energy we get from coal today comes from the energy that plants absorbed from the sun millions of years ago. All living plants store solar energy through a process known as photosynthesis. When plants die, this energy is usually released as the plants decay. Under conditions favourable to coal formation, the decaying process is interrupted, preventing the release of the stored solar energy. The energy is locked into the coal.
Coal formation began during the Carboniferous Period - known as the first coal age - which spanned 360 million to 290 million years ago. The build-up of silt and other sediments, together with movements in the earth's crust - known as tectonic movements - buried swamps and peat bogs, often to great depths. With burial, the plant material was subjected to high temperatures and pressures. This caused physical and chemical changes in the vegetation, transforming it into peat and then into coal.
Coalification
The quality of each coal deposit is determined by:
- varying types of vegetation from which the coal originated
- depths of burial
- temperatures and pressures at those depths
- length of time the coal has been forming in the deposit
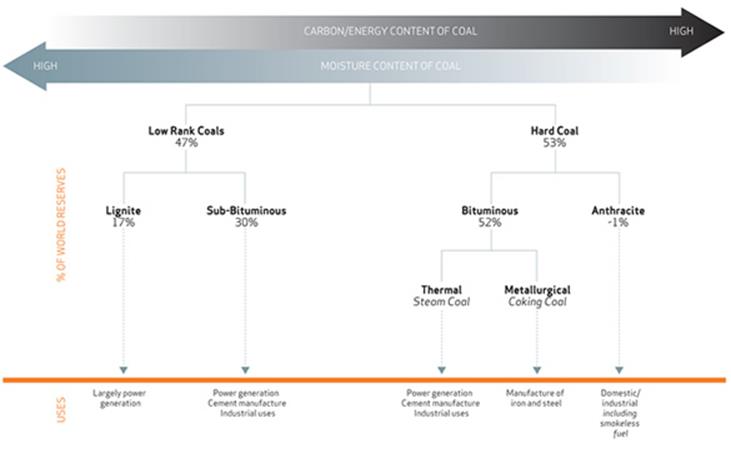
Initially the peat is converted into lignite or 'brown coal' - these are coal-types with low organic maturity. In comparison to other coals, lignite is quite soft and its colour can range from dark black to various shades of brown.
Over many more millions of years, the continuing effects of temperature and pressure produces further change in the lignite, progressively increasing its organic maturity and transforming it into the range known as 'sub-bituminous' coals.
Further chemical and physical changes occur until these coals became harder and blacker, forming the 'bituminous' or 'hard coals'. Under the right conditions, the progressive increase in the organic maturity can continue, finally forming anthracite.
In addition to carbon, coals contain hydrogen, oxygen, nitrogen and varying amounts of sulphur. High-rank coals are high in carbon and therefore heat value, but low in hydrogen and oxygen. Low-rank coals are low in carbon but high in hydrogen and oxygen content.
Coal & Steel
Steel is an essential material for modern life. The manufacture of steels delivers the goods and services that our societies need – healthcare, telecommunications, improved agricultural practices, better transport networks, clean water and access to reliable and affordable energy. Global steel production is dependent on coal. 70% of the steel produced today uses coal. Metallurgical coal – or coking coal – is a vital ingredient in the steel making process. World crude steel production was 1.4 billion tonnes in 2010. Around 721 million tonnes of coking coal was used in the production of steel.
How is Steel Produced?
Steel is an alloy of iron and carbon. Steel is produced via two main routes
- Integrated smelting involving blast furnace (BF) iron-making followed by basic oxygen furnace (BOF)
- Electric arc furnaces (EAF).
Raw Materials
Steel is an alloy based primarily on iron. As iron occurs only as iron oxides in the earth's crust, the ores must be converted, or 'reduced', using carbon. The primary source of this carbon is coking coal.
Coke Making
Coking coal is converted to coke by driving off impurities to leave almost pure carbon. The physical properties of coking coal cause the coal to soften, liquefy and then resolidify into hard but porous lumps when heated in the absence of air. Coking coal must also have low sulphur and phosphorous contents. Almost all metallurgical coal is used in coke ovens.
The coking process consists of heating coking coal to around 1000-1100ºC in the absence of oxygen to drive off the volatile compounds (pyrolysis). This process results in a hard porous material - coke. Coke is produced in a coke battery which is composed of many coke ovens stacked in rows into which coal is loaded.
The coking process takes place over long periods of time between 12-36 hours in the coke ovens. Once pushed out of the vessel the hot coke is then quenched with either water or air to cool it before storage or is transferred directly to the blast furnace for use in iron making.
Iron Making
Iron ore is mined in around 50 countries – the largest producers are Australia, Brazil and China. Around 98% of iron ore is used in steel-making.
During the iron-making process, a blast furnace is fed with the iron ore, coke and small quantities of fluxes (minerals, such as limestone, which are used to collect impurities). Air which is heated to about 1200°C is blown into the furnace through nozzles in the lower section. The air causes the coke to burn, producing carbon monoxide which reacts with the iron ore, as well as heat to melt the iron. Finally, the tap hole at the bottom of the furnace is opened and molten iron and slag (impurities) are drained off.
Basic Oxygen Furnace
The most commonly applied process for steel-making is the integrated steel-making process via the Blast Furnace – Basic Oxygen Furnace.
In the basic oxygen furnace, the iron is combined with varying amounts of steel scrap (less than 30%) and small amounts of flux. A lance is introduced in the vessel and blows 99% pure oxygen causing a temperature rise to 1700°C. The scrap melts, impurities are oxidised, and the carbon content is reduced by 90%, resulting in liquid steel.
Other processes can follow – secondary steel-making processes – where the properties of steel are determined by the addition of other elements, such as boron, chromium and molybdenum, amongst others, ensuring the exact specification can be met.
Optimal operation of the blast furnace demands the highest quality of raw materials – the carbon content of coke therefore plays a crucial role in terms of its effect in the furnace and on the hot metal quality. A blast furnace fed with high quality coke requires less coke input, results in higher quality hot metal and better productivity. Overall costs may be lower, as fewer impurities in the coke mean smaller amounts of flux must be used.
Around 0.6 tonnes (600 kg) of coke produces 1 tonne (1000 kg) of steel, which means that around 770 kg of coal are used to produce 1 tonne of steel through this production route.
Basic Oxygen Furnaces currently produce about 70% of the world's steel. A further 29% of steel is produced in Electric Arc Furnaces.
Electric Arc Furnaces
The Electric Arc Furnace process, or mini-mill, does not involve iron-making. It reuses existing steel, avoiding the need for raw materials and their processing. The furnace is charged with steel scrap, it can also include some direct reduced iron (DRI) or pig iron for chemical balance.
The EAF operates on the basis of an electrical charge between two electrodes providing the heat for the process. The power is supplied through the electrodes placed in the furnace, which produce an arc of electricity through the scrap steel (around 35 million watts), which raises the temperature to 1600°C, melting the scrap. Any impurities may be removed through the use of fluxes and draining off slag through the taphole.
Electric Arc Furnaces do not use coal as a raw material, but many are reliant on the electricity generated by coal-fired power plant elsewhere in the grid.
Around 150 kg of coal are used to produce 1 tonne of steel in electric arc furnaces.
Pulverised Coal Injection
Pulverised Coal Injection (PCI) technology involves injecting coal directly into the blast furnace to provide the carbon for iron-making – displacing some of the coke required for the process. A wider range of coals can be used in PCI, including steam coal which has a lower carbon content than coking coal. This method has a number of advantages, including reducing overall costs and prolonging the life of existing coke batteries.
Recycling
Steel is 100% recyclable. The BOF process uses up to 30% recycled steel (scrap) and around 90-100% is used in EAF production.
Source: worldcoal.org